The most effective way to improve production capacity is to reduce clerical work in engineering so your designers have more time to design.
Key Takeaways
- Thanks to frequent change orders, difficulty tracking parts, and no effective way to collect and learn from data, efficient manufacturing is difficult for Custom Machine Builders.
- Adding new staff should be the last option to increase production capacity. New staff increase operating costs and require resources such as office space, equipment, training, etc. Instead, reduce repetitive data entry and redundant paperwork to free up your current staff’s time.
- Using an ERP designed for ETO manufacturing can increase your production capacity by creating more efficient manufacturing processes and speeding up the order-to-ship timeline.
How to Increase Production Capacity
Success in our competitive market is forcing every manufacturer to make their business more responsive to client demands. The pressure is on for better, faster, and cheaper solutions. Efficient manufacturing, however, is particularly difficult for Engineer To Order companies, for several reasons:
- Customers frequently request changes to the order during or even after the design process. This can extend the length of a project and procurement efforts.
- Sales representatives need to quote projects as quickly and accurately as possible. This is problematic though, without tracking past projects and estimates to completion.
- To meet delivery deadlines, engineering needs to “pre-release” components to procurement. This, however, requires special effort to manage the bill of materials interaction with purchasing.
- The team often identifies areas where the design requires changes. Engineers then need to modify drawings as well as the Bill of Materials (BOM). Procurement will then need to adjust material orders.
- Accounting, engineering, and purchasing departments are often weighed down by unnecessary clerical work.
These are just a few of the quirks that make Custom Machine Builders so valuable but so busy. While it may seem impossible, you can improve the level of service to your customers while increasing your production capacity. Furthermore, you can do so without adding staff!

More Efficient Manufacturing
By streamlining your business processes, you’ll free up critical staff from clerical tasks to focus on income-generating work. Inherently, Engineer To Order companies have talented staff, often creative and passionate. Unfortunately, as most managers know, their key staff are burdened with significant clerical responsibilities. It’s common for Custom Machine Builders to see the potential to expand their sales but not have the resources to do so.
We know from our own experience as machine builders and see confirmation from Automation.com that “Engineers are highly paid professionals who suffer when performing repetitive functions, such as back-and-forth massaging and frequent manual design adjustments. Only with a good marriage of engineering and sales automation can ETO (Engineer To Order) manufacturers provide rapid responses and compelling quotes to customers”.
Usually, creating more efficient processes in your manufacturing requires additional staff or workspace. However, you can make improvements without these resources.
Would Hiring Additional Staff Help an ETO Manufacturer Grow
Increasing capacity by adding new staff should be the last option for a manager. New staff will immediately increase operating costs through hiring expenses, fees, and salaries. Additional staff will also require resources such as office space, equipment, training, and supervision.
Moreover, employees that don’t stick around can be costly. Even a successful new employee, particularly in key technical departments such as engineering and manufacturing, still requires many months of experience before they can be 100% productive. That’s why it’s recommended you improve and maximize your current resources before adding to them.
How to Improve Production Capacity
Freeing up existing staff from clerical duties is the most profitable option. Consider your engineering department. Designers typically spend 50% of their time reissuing drawings and rewriting BOMs. They need to communicate with purchasing, process change orders, issue lists, and reports. Meeting with sales and manufacturing adds to their day as well. Finding a way to free up even 25% of their time has the effect of increasing your engineering capacity. Your four designers now have the capacity of five experienced designers.
The impact of freeing up design capacity has a multiplying effect on your manufacturing capacity. For example, for many Custom Machine Builders, their shop staff is four times the number of designers. Increased engineering capacity results in more shop hours sold. This chain reaction increases company profits with a minimal increase in fixed costs.

How to Reduce Material Costs
Speeding up the design process helps reduce material costs. Engineer To Order (ETO) businesses usually define the materials required after they get the client’s order. Because this is a creative process… and changes from the client do occur, it is not unusual for engineering to need more time than what was scheduled. This means that procurement has less time to buy the materials to meet promised deliveries.
Time constraints reduce or eliminate the possibility of price shopping. The procurement department could save significant amounts of money if it had access to the BOM sooner (and had time to solicit competitive bids). In a $10 million / year sales firm, spending $4 million in materials, a 3% gain (with competitive bidding) alone represents $120,000 annually. Here, you can start to see how valuable enterprise resource planning software or manufacturing software can be for Custom Machine Builders. It connects engineering to purchasing and the shop floor.
As Nate Hinks, former Director of Sales at Farason said: “Total ETO has streamlined our purchasing process and saved us the cost of one full-time purchasing agent”. Learn more about the improvements Farason experienced when integrating Total ETO with SolidWorks.
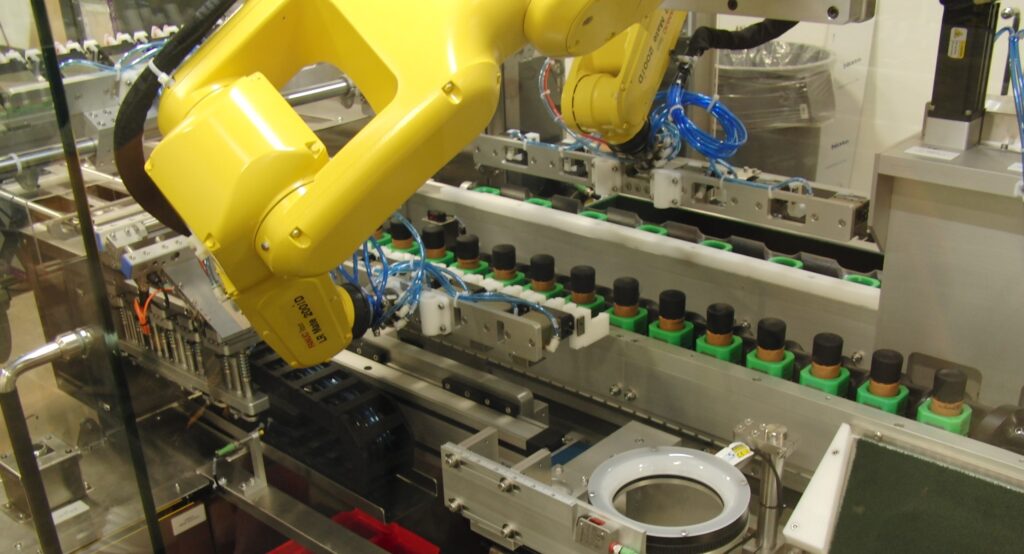
Another major consideration in efficient manufacturing is using your history to reduce new engineering. Implementing a system that allows staff to reuse information from prior projects can not be over-emphasized. The ability to quote clients based on similar past projects not only improves the accuracy of estimates but also reduces the time spent quoting and qualifying clients.
Simply said, estimating is the act of determining how much time and money is needed to complete a project. Recognizing that estimating is ultimately an attempt to predict the future helps you see that the more info you have, the better. Like any projection, the accuracy of the estimate improves with the availability of more data.
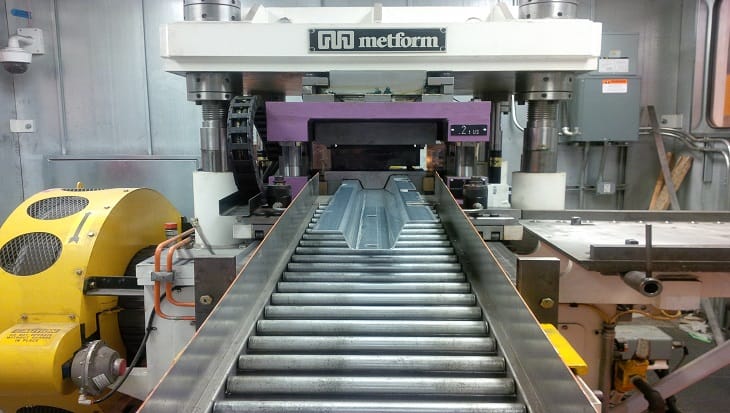
Metform International has been providing roll-forming machines and coil-processing equipment for over 45 years. Purchasing & Logistics Manager Tom Hirschler started seeing the benefits of their sales team using an Engineer To Order ERP right away; “Total ETO has given us the tools to win bids successfully and become a worldwide competitor”. More details about the benefits Metform is still experiencing, including streamlined data and fast-tracked spare parts orders, are available in this success story.
A Bright Future for ETO Manufacturers
Many manufacturers are currently struggling and as we’ve learned, Custom Machine Builders are all too familiar with this battle. We can see though, that the right ERP (one that is designed for Custom Machine Builders) can be counted on to save time and money throughout an organization. The right ERP really can increase production capacity by creating more efficient processes in manufacturing. Additionally, this kind of manufacturing software can reduce the engineering work required and speed up the order-to-ship timeline.
Written by Taylor Dykstra